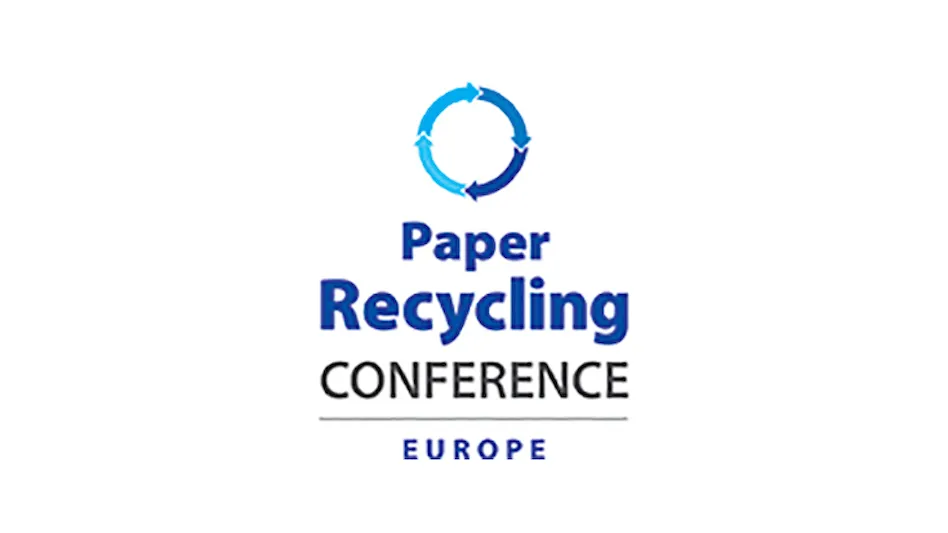
Separating commingled recyclable materials requires constant attention and ongoing dialog, according to panelists at a 2015 Paper Recycling Conference Europe session titled “Recycling Plant Optimisation.” The conference took place in late October in Madrid.
Neil Arlett, division engineering manager with United Kingdom-based Biffa Group Limited, said the company handles some 200,000 tonnes per year of recovered fibre, much of it flowing through its two large material recovery facilities (MRFs) in London and Aldridge, England.
The MRFs handle material collected by Biffa from a variety of sources, including many town council recycling programs, said Arlett. The material arrives in high volumes, but inbound fibre can have contamination rates as high as 16%, according to Arlett.
“We are recycling more material than we’ve recycled before,” said Arlett, but to improve the quality is an ongoing task. Paper mill customers will typically not wish to contend with contamination levels greater than 1% to 3%.
Some solutions are mechanical, said Arlett, who described an initiative at Biffa’s MRFs to change the spacing on disc screens that separate two dimensional materials (paper) from three-dimensional ones (bottles, cans and contaminants).
Dialog is another key component toward improving quality, with Arlett saying there is nothing easy about informing a town council that the material it is collecting is so contaminated that it is more of a hindrance toward recycling rather than a way of saving the planet.
Herman van der Meij of U.K.-based Viridor says his company continues to invest in upgrades to improve the quality of the 2.2 million tonnes of recyclable materials it handles each year.
He said Viridor’s 25-year contract with the Greater Manchester Combined Authority in England has achieved results that “are brilliant,” as the length of the contract allows Viridor to earn return on investments in its recycling facilities, and the contract was “a way to move recycling up the government agenda” in Manchester.
Viridor, like Biffa, is engaged in ongoing dialog with material generators (including town councils) and it also monitors quality to the point of labeling and time-stamping the bales produced at its plants. “Yes it costs money,” said van der Meij, but the tactic fosters accountability, he stated. “We can identify what went wrong and stop problems at the gate,” added van der Meij.
Panelist Andy Cui from the Shanghai office of Sweden-based packaging producer Tetra-Pak provided an overview of that company’s efforts to boost the recycling rate of its multi-material beverage cartons.
Cui said in China, as it has in other countries, Tetra-Pak has worked to identify paper mills that can pulp the multi-material juice and beverage cartons, which typically consist of 75% paper, 20% plastic and 5% aluminium. Mills that produce non-white “away-from-home” tissue products are ideal candidates, he said.
Tetra-Pak said the 25% non-fiber portion can be retrieved from the drum screens at paper mills and treated through a heating, chemical and mechanical process to create a pellet that can be used by “various manufacturers.” Added Cui, “This is necessary to make the whole [effort] cost-effective.”
The 2015 Plastics Recycling Conference Europe event was Oct. 28-29 at the Eurostars Madrid Tower Hotel in Madrid.